The Business Situation
Global Finishing Solutions (GFS) based in Osseo, Wisconsin, is a leading global provider of finishing solutions and paint booths within the automotive, industrial, aerospace, and defense markets, among others. More than 325 employees contribute to GFS’s success in several locations across the US and in Canada.
Analyzing service history and equipment performance data, GFS determined more than 80% of service calls were associated with filter maintenance issues. Many times, GFS service technicians would incur expensive travel to customer facilities to discover filter failure caused by basic usage or environmental factors. Industry standard filter service recommendations had always been for calendar-time based filter service and replacement, all predicated on simple assumptions of operating hours, number of shifts and finishing processes. Their initial analysis found that for some customers, filters were reaching full load and clogging earlier than standard change intervals, causing paint and equipment issues. Often, filters were not being maintained properly, resulting in reduced airflow inside the paint booth and negatively affecting productivity, quality, and shop revenue. In some instances, it cost end-users $3K to $5K for every hour of lost paint booth production.
GFS needed a more accurate way to measure performance of the overall system, starting with filter usage parameters. With more accurate, real-time data, they knew they could help customers maximize filter performance and reduce costs. Identifying use and environmental variables affecting reduced filter life and booth performance would have direct bottom line effects for customers.
Having accurate usage data in real-time meant they could advise customers to address filter changes before they negatively impacted production and spray booth performance, avoiding more severe heating system failures, damage to fan plates, or catastrophic failure of painting equipment and ductwork. Defining the proper replacement schedule for each customer’s use case would improve their efficiency, performance, and profitability. The solution they were searching for would have to inform both GFS personnel and customers of equipment and filter performance trends, allowing them to identify performance issues, then plan and schedule a maintenance event. Decreasing unplanned downtime and improving maintenance turn-around time would maximize paint booth returns for GFS customers. Click to read the solution, business impact, and what’s next for GFS utilizing the Scante IoT-CX system.
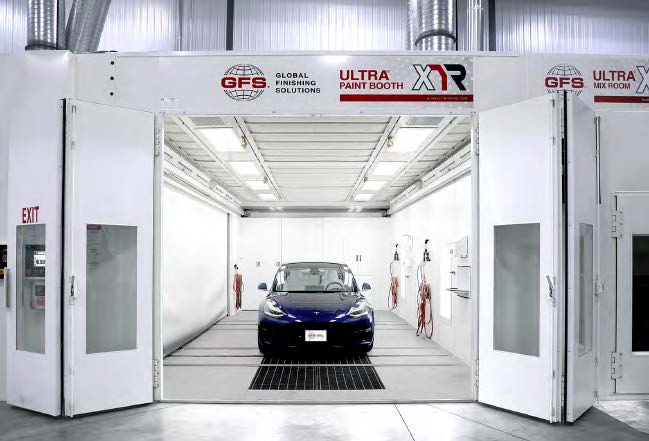